wibas
Zusammen machen wir Ihre Organisation lieferfähiger.
Wir bieten langjährige Erfahrung in der Beschleunigung von Produktentwicklungs-Prozessen und der Verkürzung von Durchlaufzeiten – sowohl für Dienstleistungsorganisationen als auch in der Entwicklung und Produktion. Unsere Expertise liegt in der Entwicklung und Implementierung nachhaltiger organisatorischer Verbesserungen, die den spezifischen Anforderungen Ihrer Branche gerecht werden.
Unsere Dienstleistungen
Mit einem klaren Fokus auf die Verbesserung der Lieferfähigkeit unterstützen wir Sie mit maßgeschneiderten Workshops, praxisorientierten Schulungen, zielgerichteter Beratung und nachhaltiger Begleitung.
Wir unterstützen die konkrete Umsetzung identifizierter Maßnahmen und begleiten Ihre Organisation dabei, neue Ansätze dauerhaft zu verankern. Durch unser schrittweises und ergebnisorientiertes Systemisches Change Management stellen wir sicher, dass Verbesserungen messbare Resultate liefern und langfristiges Wachstum unterstützen.
Bausteine Lieferfähiger Organisationen
Kontaktieren Sie uns oder vereinbaren Sie direkt einen Termin mit unserem Kundenteam. Wir freuen uns darauf gemeinsam Ihre Organisation weiterzuentwickeln.
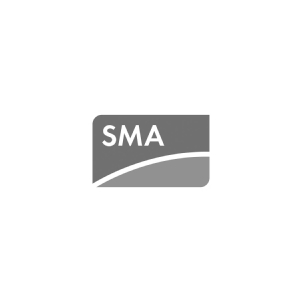
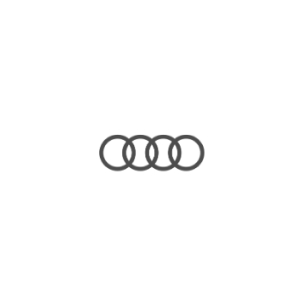
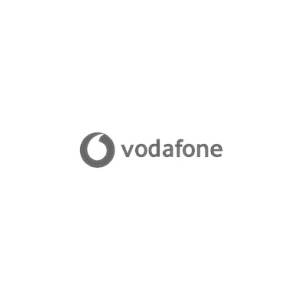
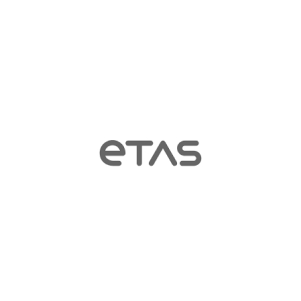
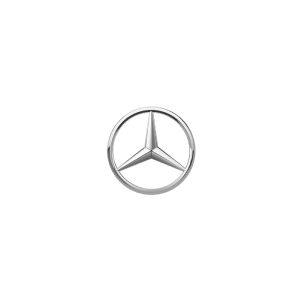
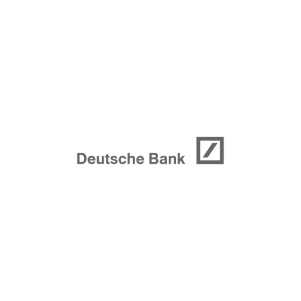
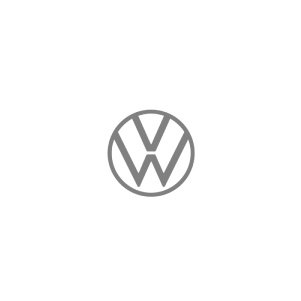

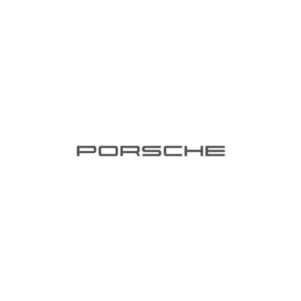
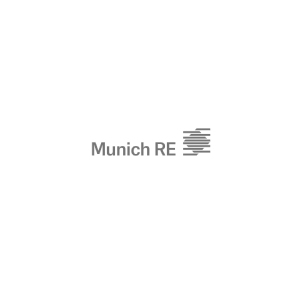
Kundenbeispiele
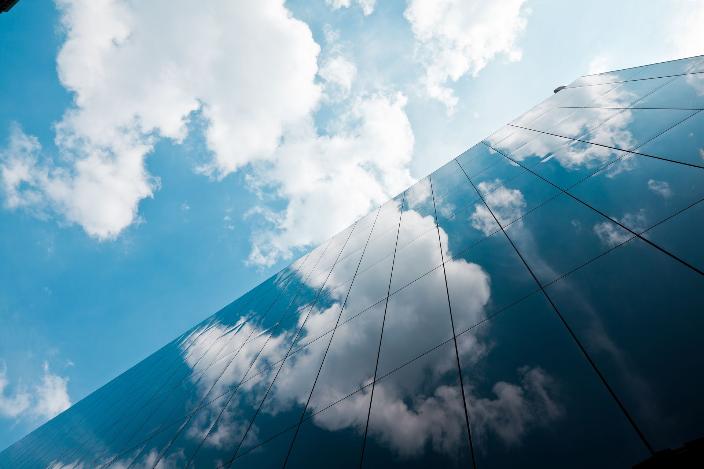
Agile Transformation bei der dwpbank
Begleitung eines agilen Großprojekts und Einsatz von Interims Agile Coaches zur schnelleren Lösungs- und Servicelieferung der dwpbank.
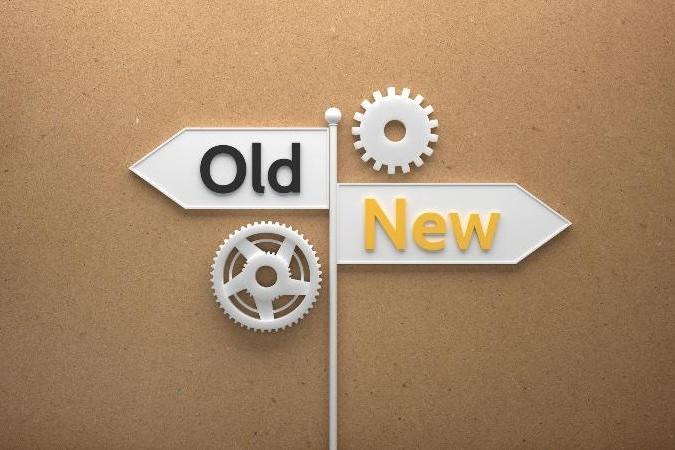
Produkt-Entwicklung bei Merck
Etablierung eines strategisch ausgerichteten agilen Produktentwicklungsprozesses und Team-Begleitung durch agile Zusammenarbeits-modelle.
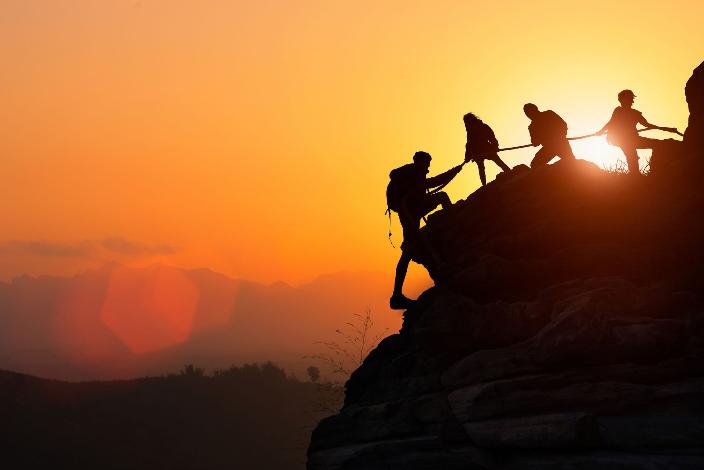
Strategie-Entwicklung bei E-T-A
Entwicklung eines selbstorganisierten Teams, Umgang mit wechselnder Teambesetzung und evolutionäre Einführung von Kanban.
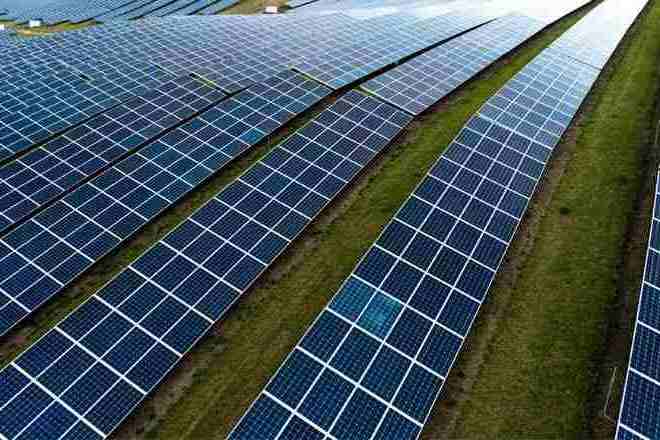
Einführung von SAFe® bei SMA
Erfahrungsbericht über die Einführung von SAFe bei SMA – Herausforderungen, gegangene Schritte und positive Auswirkungen für ein Unternehmen der Energiebranche.
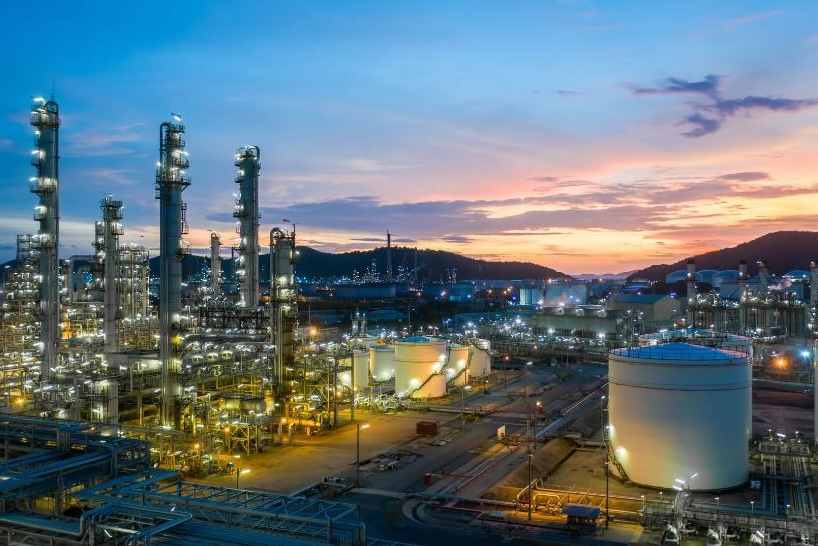
Change in der chemischen Industrie
Etablierung einer agilen Arbeitsweise sowie Etappenplanung und Einführung einer Portfolio-Ebene zur Vermeidung kontinuierlicher Überlastung.
Kommende Events
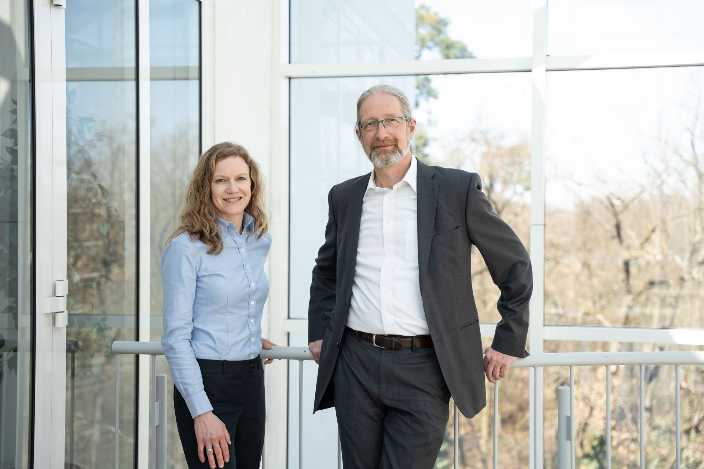
25.09.25 Abendevent: Lieferfähigkeit unter gegebenen Rahmenbedingungen
In unseren Abendevents stellen wir einzelne Bausteine von lieferfähigen Organisationen vor. In diesem Modul geht es darum, wie man mit gegebenen Rahmenbedingungen in einem veränderlichen Umfeld umgehen kann und welche Haltung man einnehmen sollte. Von 17:30-19:00 Uhr.
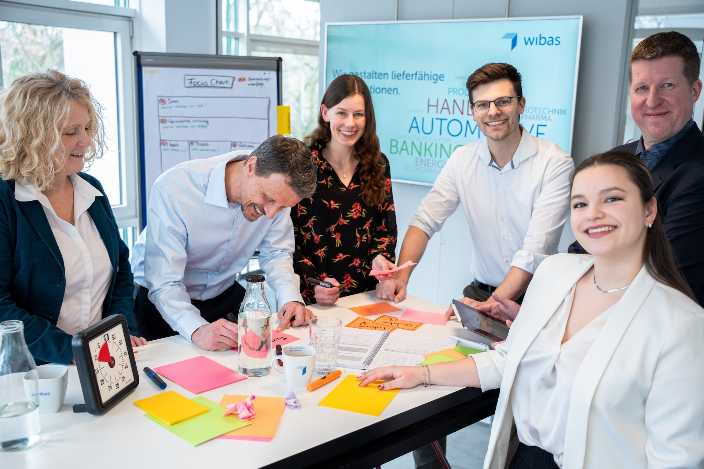
03.09.25 Kanban Sprechstunde
Haben Sie Fragen zu Kanban oder Arbeitsfluss? Hier finden Sie Antworten auf Ihre Fragen. Unsere Kollegin Astrid Meyser bietet jeden
ersten Mittwoch im Monat eine Kanban Sprechstunde an. Hier können alle ihre Fragen zu Kanban, der Einführung oder Etablierung eines Systems, Kennzahlen oder Verbesserungspotenziale diskutiert werden.
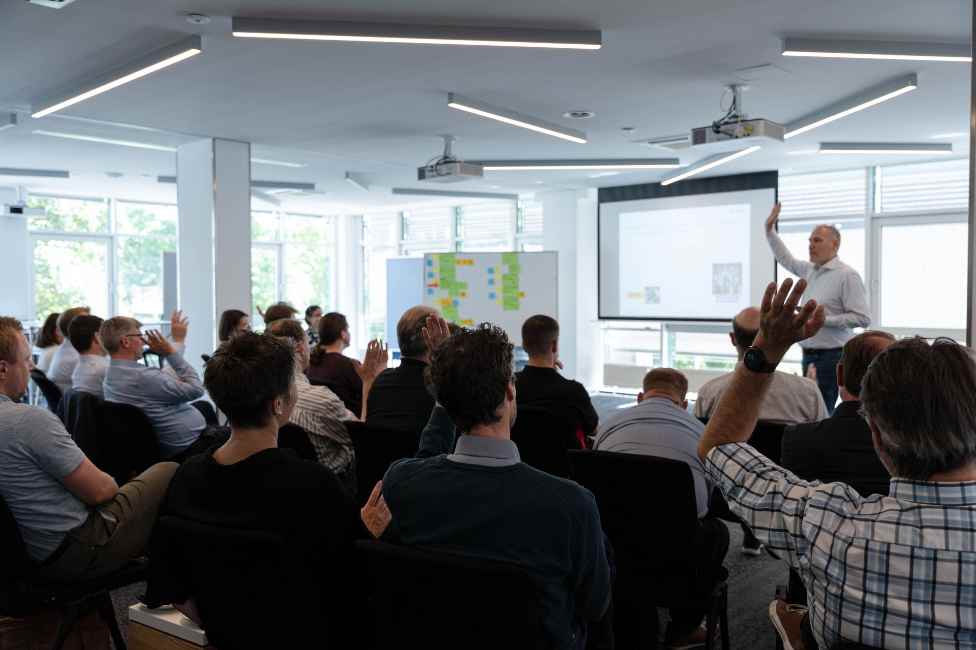
18.11.25 Meetup: Agilität in der Entwicklung & Produktion physischer Produkte
m November ist es wieder soweit: unser Meetup Agilität in der Entwicklung und Produktion physischer Produkte, welches wir mit vielen Teilnehmern im vergangenen Jahr erstmals durchgeführt haben, findet zum 3. Mal in Darmstadt statt von 13-18 Uhr. Die Teilnahme ist kostenlos.

30.09.25: VKU Stadtwerke Kongress in Mainz
Dieses Jahr sind wir vom 30.09. bis 01.10.25 auf dem VKU Stadtwerkekongress in Mainz dabei. Dies ist der zentrale Branchentreff für Innovation, Austausch und Impulse. Dort treffen sich jedes Jahr die Entscheider:innen der Kommunalwirtschaft und diskutieren aktuelle Herausforderungen und präsentieren praxisnahe Lösungen. Wir freuen uns über Ihren Besuch an unserem Stand und unserer Session.
Hilfsmittel und Assets

Self-Assessment Change
Bewerten Sie ihr eigenes Change Projekt. Sie erhalten eine Einschätzung in Bezug auf Erfolgsfaktoren für einen Change. Darüberhinaus erhalten Sie Empfehlungen, welche Maßnahmen Ihren Change nachhaltiger und effektiver gestalten können.

Self-Assessment Lieferfähigkeit
Bewerten Sie die Lieferfähigkeit Ihrer Organisation. Sie erhalten Empfehlungen, welche Maßnahmen ihre Organisation auf dem Weg zu mehr Effizienz, mehr Effektivität und mehr Kundenorientierung unterstützen können.

Umfrage zum Thema Prozessverbesserung
Nehmen Sie an einer kurzen Umfrage zum Umgang mit Prozessverbesserung in Ihrer Organisation teil. Einmal im Monat verlosen wir unter den Teilnehmern unseren Bestseller: "Organisation in einer digitalen Zeit."
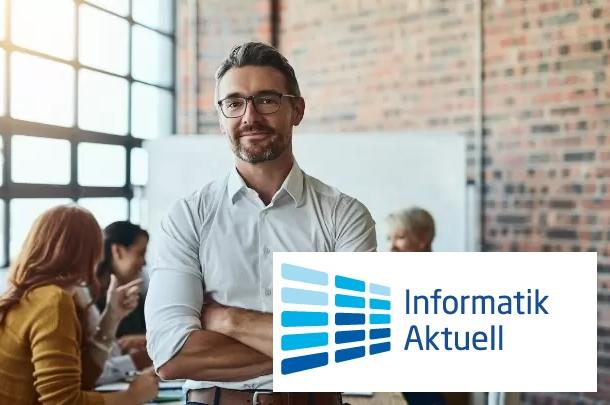
Toyota Lean Leadership: Leadership in Complexity
Das Toyota-Lean-Leadership-Modell hilft Führungskräften, in der VUCA-Welt mit Klarheit, Lernfähigkeit und Agilität zu bestehen. Lesen Sie hierzu diesen aktuellen Artikel von unseren Kolleginnen Tina Eisoldt und Caroline Haußmann in der Informatik Aktuell.
Schulungen
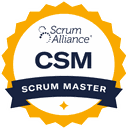
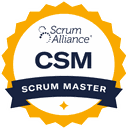
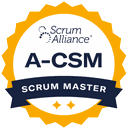
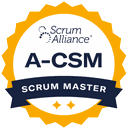
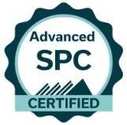
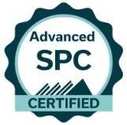
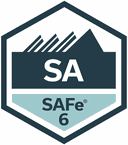
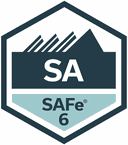
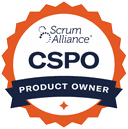
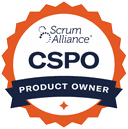
Frühbucher
gilt bei einer Anmeldung bis zu vier Wochen vor Schulungsbeginn
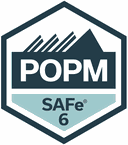
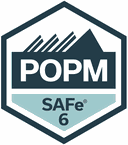
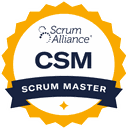
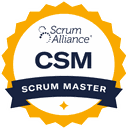
Frühbucher
gilt bei einer Anmeldung bis zu vier Wochen vor Schulungsbeginn
Lieferfähige Organisationen
Lieferfähigkeit und Kundenorientierung sind entscheidende Merkmale für den Erfolg jedes Unternehmens. Lesen Sie hier vorauf es ankommt.
Themen
Wir gestalten lieferfähige Organisationen mit den jeweiligs passenden Werkzeugen. Hier finden sich eine Auswahl unserer Werkzeuge und Themen.
Beratung
Wir sind eine Unternehmensberatung. Wir coachen Teams, beraten Führungskräfte und gestalten Transformationen.
Publikationen
Unser Wissen, in Publikationen und Materialien so aufbereitet, dass Sie es für Ihre Arbeit im 21. Jahrhundert nutzen können.
Akademie
Wir geben unser Wissen auch im Rahmen von Schulungen weiter. In unserer Akademie finden Sie Schulungen zu Scrum, Kanban, Agiler Führung, Scaled Agile und vieles mehr.
Karriere
Bewirb dich bei uns. Wir freuen uns auf dich. Bei uns findest du Jobs, die Unternehmen von morgen gestalten. Und dich erwartet ein engagiertes und cooles Team.
Über uns
New Consultancy for New Work: Wir sind eine moderne agile Unternehmensberatung für Arbeiten und Wirtschaften im 21. Jahrhundert.
Ist immer für Sie da:
wibas GmbH
undefined