Constant change has become the norm for companies and presents managers with completely new challenges. A key question here is how companies can organise themselves in such a way that they can react quickly to new requirements without losing efficiency.
One possible lever here is Kanban. But what difference can the use of Kanban make to corporate management?
–
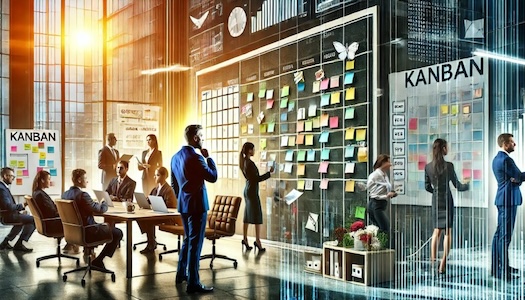
What does flow mean in everyday life?
‘Flow’ describes a state in which work runs smoothly and without interruption. This term is used in many areas. In everyday life, we experience flow when we are completely absorbed in a task, such as at work, during sport or hobbies. In this state, we often feel particularly productive because the effort and the result are perfectly balanced.
Lean and Kanban: efficiency through continuous improvement
In the business world, the term ‘flow’ has a more specialised meaning, especially in the context of Lean and Kanban.
Lean management, which originally comes from automotive production, attempts to reduce waste, i.e. to eliminate non-value-adding process steps. – Be it unnecessary waiting times, superfluous work steps or overfilled warehouses. Kanban, a lean management method, visualises the work flow and thus helps to identify bottlenecks, among other things. This transparency facilitates continuous process improvement, for example by limiting work in progress (WIP). These so-called ‘WIP limits’ prevent Kanban from starting too many tasks at the same time. This immediately encourages a focus on the activities that are currently being actively worked on. – This in turn means that this work flows through the system faster, i.e. it is completed more quickly. Both Lean and Kanban help to organise work processes in such a way that the value stream from idea to delivery functions as smoothly as possible and continuous improvement is supported.
Value stream and value chain: a brief overview
A value stream comprises all the steps required to take a product or service from idea to delivery. This is similar to the value chain, which describes the sequence of activities through which a company creates value. Both concepts emphasise the importance of improving the flow from start to finish to maximise efficiency and value for the customer. By looking at the entire process, local optimisation is avoided and the overall delivery capability of the company is improved.
Concepts and measurements from series production
In production, methods have been developed to measure and improve flow. Concepts such as throughput, cycle time and WIP (work in progress) are important for understanding the efficiency of production processes. These concepts can also be applied to knowledge work. However, some adjustments are necessary here as the work is less predictable and often more complex.
Perfect flow: reality or wishful thinking?
“Perfect flow” means that work moves smoothly from one phase to the next, without delays or interruptions. In mass production, this is achievable because the processes are standardised and repeatable. In knowledge work, as described in the book ‘Project Phoenix’, perfect flow is harder to achieve because creative and intellectual tasks often contain unpredictable elements. Nevertheless, managers can achieve great improvements by applying lean and Kanban principles.
Kanban is key to company coordination
Kanban offers a flexible and visual method for coordinating flow at all levels of an organisation. By visualising tasks and bottlenecks, managers can react quickly to problems and risks and make the necessary adjustments. This leads to a more efficient way of working. Kanban also ensures greater transparency and better communication within the organisation.
SAFe® (Scaled Agile Network), which sees itself as a systematic approach to scaling agile practices at company level, also uses Kanban as a tool for corporate management, for example for portfolio management.
Why Kanban makes a difference for managers
So, why does Kanban make a difference for managers?
By using Kanban for company coordination, it is firstly possible to better visualise active and upcoming projects and thus make better decisions. One of these decisions can be, for example, following the Kanban idea of finishing things before starting new ones. This minimises work in progress and promotes flow, which leads to smoother and faster delivery. This can significantly increase a company’s ability to deliver.
Flow not only improves efficiency, but also employee satisfaction and the quality of work. If managers optimise the flow in their value streams, they can strengthen the adaptability and resilience of their organisation. This is particularly valuable in uncertain times like these.
Curious? Let’s see together how we can take your organisation’s delivery capability to the next level.
You can also take a look at our website, for example on the topics of leadership development, corporate strategy and portfolio management or our training courses, for example our certified Kanban training courses.
If you have any questions or suggestions…
Feel free to contact us.